

The measuring system generates an error signal for deviations greater than +2%. The light intensity received is compared against the standard value (70%). Sender beam intensity changes between 70 and 100% during control value determination. A warning signal is generated when the “zero value” is outside the specified range.
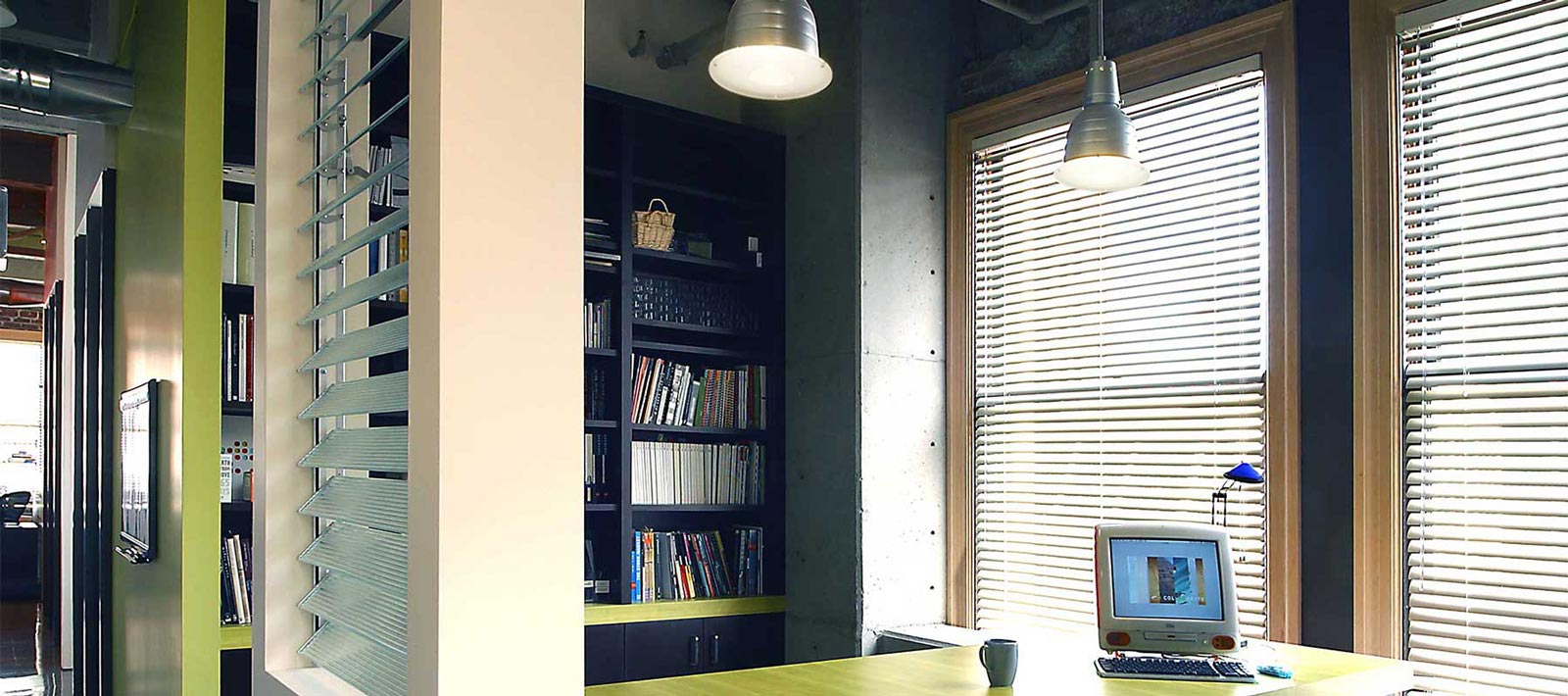
This means possible drifts or zero point deviations are detected reliably in the overall system (e.g. The sender diode is switched off for zero point control so that no signal is received. Every 90s (standard value) output of values determined (duration parameter can be modified.The measuring time depends on the increase in contamination value (change > 0.5% – measurement is repeated up to 2 times). 45 s measurement of zero value, control and contamination of the optical interfaces. A function check triggered manually can help localise possible error causes should a device malfunction occur. Any unallowed deviations from normal behaviour that may occur are signalled as errors. The calibration coefficients determined can be entered directly in the measuring system as numerical values.Ī function check can be triggered at fixed intervals as from a definable starting timepoint for an automatic function check of the measuring system. Scattered light intensity not only depends on the number and size of particles but also on the optical characteristics of the particles and therefore the measuring system must be calibrated using a gravimetric comparison measurement for exact dust concentration measurement. Measure scattered light intensity is proportional to dust concentration. The measuring volume in the gas duct is defined through the intersection of the sender beam sent and the receive aperture.Ĭontinuous monitoring of the sender output registers the smallest changes in brightness of the light beam sent which then serves to determine the measurement signal. A highly sensitive detector registers the light scattered by the particles, amplifies the light electrically and feeds it to he measuring channel of a microprocessor as central part of the measuring, control and evaluation electronics. A laser diode beams the dust particles in the gas flow with modulated light in the visual range (wavelength approx. The measuring system works according to the scattered light measurement principle (forward dispersion).
